Finishing off the 3D printer cabinet

There's a bit more work needed to finish off the 3d printer cabinet. This should be done as part of the extraction works so we don't have to shift everything out and in again.
Work needed - building:
-
Adding doors to the front of the cabinet (see subtasks below)
-
Adding an extra level of French cleats for spool storage
-
Building a trolley for the XL
-
Building an enclosure for the XL ( @Sophie Murday is printing the parts for this from ABS)
-
Routing air extraction from the trolley into the cabinet
-
Build trolley for the sandblaster at the same time as they'll have essentially the same design
-
Sanding down all exposed wood surfaces
-
Filling any cracks
-
Sealing the exposed wood
Work needed - electrical:
-
Replacing the relays with a better electrical solution that has an actual API ( @Penny Wood is acquiring Sonoff relays)
-
Bonus: Provide remote controlled GPOs for the rest of the e-lab.
-
Adding LAN points for the printers (and possibly the relays too)
For the doors, I am thinking the best option would be sliding doors. While opening doors on hinges were my original consideration, I feel four doors on two tracks means you can access half the cabinet easily at a time and can leave them open without risk of them being knocked off or getting broken.
Adding tracks to the existing cabinet is going to be slightly tricky, ideally the tracks would be rebated into the wood frame but this will require partial disassembly of the bench and may need some screws to be changed around. Alternatives are to just screw the tracks to the benchtop, possibly with a timber moulding around it, or make a framework for it that attaches to the front of the cabinet. The front framework would have the advantage that it potentially would look nicer, plus it gives just a bit more depth to the cabinet that way, but it is more work too. We also need to consider how to get the doors in place once built, and being able to replace doors if they get badly scratched or broken.
Work needed - doors:
-
Source materials (see below)
-
Cut acrylic for doors, including laser-cutting holes for handles
-
3D print flat cut-out handles for the doors and install
-
Install aluminium frame around doors
-
Figure out and install tracks in doors
-
Place doors into tracks
-
May need to add supports for the benchtop in the centre
Inventory of parts required
-
More 75x30 framing pine. There is some left over but probably not enough.
-
DAR 42x19x3m x2 (French Cleats)
-
Heavy-duty and lockable caster wheels x8 (may be able to salvage 4 from broken trolley)
-
Heavy-duty wood sealing. I have used carbothane clear a lot in the past with good results
-
Painting equipment and solvent for cleanup
-
Acrylic panels for doors - Penny to measure doors.
-
Aluminium c-channel frame for the doors
-
Aluminium track for the doors to run through - possibly with ball-bearings for easy slide
-
Relays, we discussed this and think the Sonoff 4ch pro are the best in terms of price and ease of use
-
Ethernet switch and cabling (I suspect a 100kps switch is probs plenty, GB upstream though)
-
Ethernet wall plates x4
Item removed
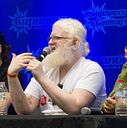
Fletcher Boyd Sun 5 May 2024 10:19AM
Agree re: tracks mounted to front rather than inbuilt as best option
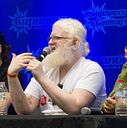
Fletcher Boyd Sun 5 May 2024 11:19AM
Reckon we could add a third row here thats rails but no boxes for filament that hasn't been opened yet?
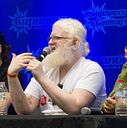
Fletcher Boyd Sun 5 May 2024 11:29AM
tbh while asking this I did forget that the lower tiers would be larger than they are now due to the lid etc

Penny Wood Sun 5 May 2024 11:43AM
@Fletcher no, only two rows will fit unfortunately. It wasn't going to work otherwise
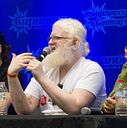
Fletcher Boyd Sun 5 May 2024 11:44AM
@Penny Wood Ah damn, I'll explore other options then. It looks like our on hand filament is going to be larger than the storage available above the bench

Penny Wood Sun 5 May 2024 12:07PM
Oh... maybe just rails will fit? Would have to check
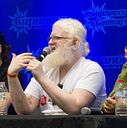
Fletcher Boyd Sun 5 May 2024 12:34PM
If you get a chance that would be great :)
-
✔️
@Penny Wood to investigate height of minimalist storage above planned filament boxes for unopened spools

Penny Wood Sun 5 May 2024 12:54PM
There's 730 space between the top of the cabinet and the roof. The spool boxes are 230 high as designed currently, and need absolute minimum clearance of 20 above to clip onto the cleats, so 500 all up. There's an extra 10 below the bottom box, which leaves 220 left. Maybe if you absolutely made the rack right up against the roof it would be possible, but it's cutting it very fine. You also have to clear over the rail to get it into the rack, and we have to have at least some clearance height or the spools will fall off. I dunno, seems super sketchy, would be down to the absolute millimeter.
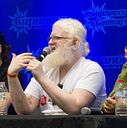
Fletcher Boyd Mon 6 May 2024 1:21AM
@Penny Wood can you send the exact dimensions of the acrylic required for the doors, we have an opportunity to get in on an upcoming acrylic order.

Penny Wood Mon 6 May 2024 1:54AM
@Fletcher as in a sheet to cut all the doors? or each individual door? I won't be back in the space until Weds, but can get it off the model. Will probs want 10-15mm overlap between each door, so width + 30-45mm + kerf. Width is a shade under 2.4m, My memory tells me 2386, but would have to check to be sure. Alternately if you're there you could measure it.
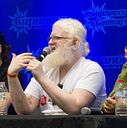
Fletcher Boyd Mon 6 May 2024 2:01AM
@Penny Wood so by the sounds of it we'll need two sheets. I'll measure etc Wednesday night.

Penny Wood Mon 6 May 2024 3:22AM
@Fletcher Should also ensure we can get appropriate track and frame for roller doors before ordering anything. Not something I'm familiar with.

Penny Wood Wed 8 May 2024 10:15AM
Just looking at how to do the doors. In discussion with Fletcher he thinks the acrylic can just run in the tracks without rollers or anything, possibly with a 3d printed skid. Found appropriate tracks here: U-CHANNEL | Extrusions Online which would suit 6mm acrylic I think.
Another option is this one from Bunnings. It's quite cheap, but not long enough. Could probably get two and run them side to side, but would need to align it carefully.
If anyone has done this before and has something that works, input appreciated.
Sophie Murday · Sun 5 May 2024 2:20AM
I think attaching the doors to a front framework is a good option, it means you could have a stopper block at the end that’s removable to slide out broken doors. The main bench enclosure doesn’t need to be particularly airtight, it’s just a draught shield, so having it sitting slightly in front of the front of the sides shouldn’t matter