Air Extraction

I'm thinking about how to organise the extraction for the e-lab. This will include air extraction from:
New 3D printer cabinet
Side enclosure for the XL
Extraction from soldering workstation
? extraction from the resin printers
The plan is to run air conduit up the back of the new cabinet and other areas, through air duct, and up the wall. Vent would be through the apex of the roof in the corner next to the wall.
Parts needed:
-
Ventilation grille(s) for the back of the cabinet
-
✔️
Air conduit - I have quite a bit in my roof as part of a decommissioned air filtration system
-
Connector to run conduit through ceiling
-
✔️
Conduit manifold - will be needed if we have multiple entries
-
? Conduit valves. Do we want to have separate zones for extraction or does it not matter?
-
Air pump / fan
-
Less ugly air conduit to go between the cabinet and the XL enclosure, possibly with magnetic attachment points
I've done a bit of research on airflows required for fume extraction, a face wind of about 0.5 m/s is suggested. Calculation for the cabinet with half the doors open half-open that's 1.2m x 0.6m x 0.5 m/s = 0.36 m^3/s = 360 L/s = 21.6 m^3/hr. Happy to be corrected on this if someone knows more about it.
Even the cheapest Bunnings bathroom extractor fan is more than adequate for the task. For comparison, the cheapest fan at $29 moves 290 m^3/hr, so if anything, we'll have too much air movement and may need to PWM control the fan to not move excessive air. We can get wall-mounted inline fans from ali-express for around $40.
Yeh, the above is all wrong! Mistake in calculation there. 1.2m x 0.6m x 0.5 m/s * 3600 s/h = 1,300 m^3/hr.
In terms of construction required to move forward, I won't scope any other fume hoods at this point, that's probably for later, although I think having the manifest installed is a good idea. Which means building required:
-
Make workspace above the e-lab safe for working on. No more accidents please!
-
Mount grille(s) in back of cabinet
-
Cut hole in ceiling
-
Fit ceiling connector
-
Mount manifold
-
Run conduit from grille to ceiling and to manifold
-
Mount air pump
-
Mount exit point in roof
-
Run conduit from manifold to pump and to the roof
Running concurrently with / part of this project will also be finishing off the cabinet and making a trolley for the XL, but I'll put this in a separate thread.
Comments?
Item removed

Penny Wood Sun 5 May 2024 2:13AM
OK that was quite successful. 17 m of duct, 2x three-way manifolds and 1x four-way manifold
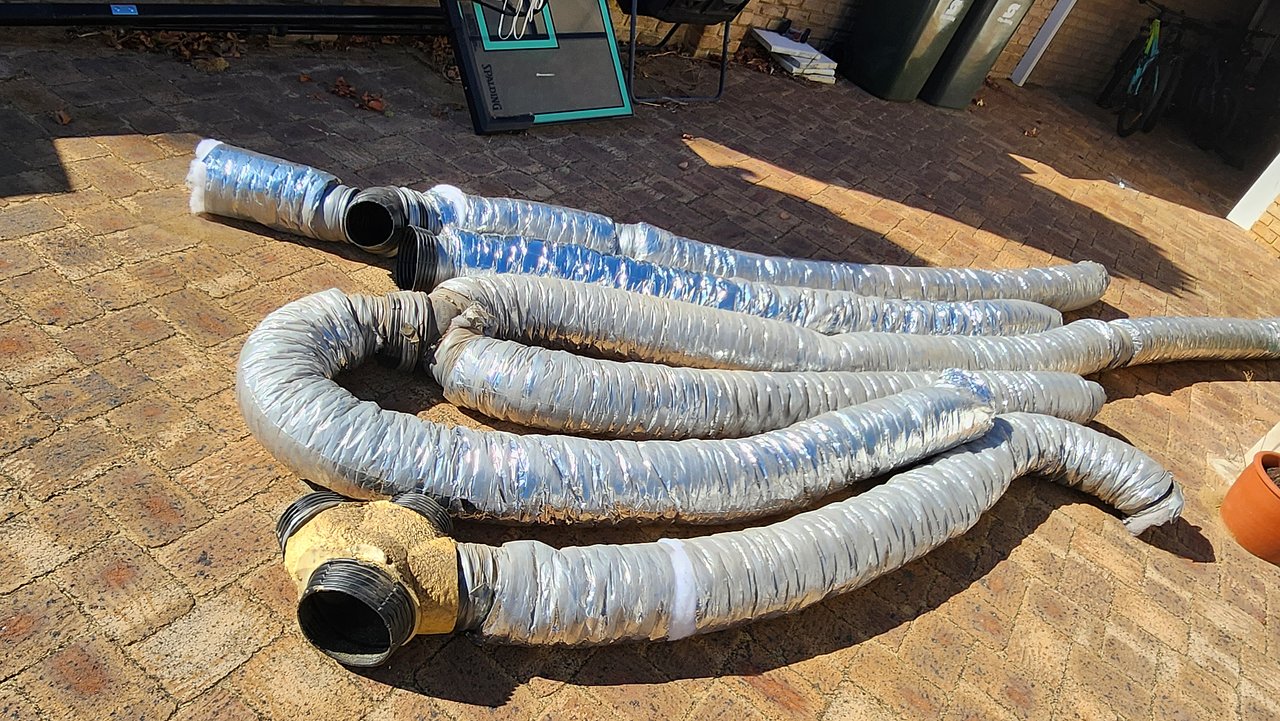

Penny Wood Sun 5 May 2024 2:14AM
There is also this thing, I don't know how useful it would be though, it's an old air filtration system that all the duct goes out from. It will be a total PITA to get out though, would probably have to take some tiles off and I'm not even sure it would fit between the tiling timber,
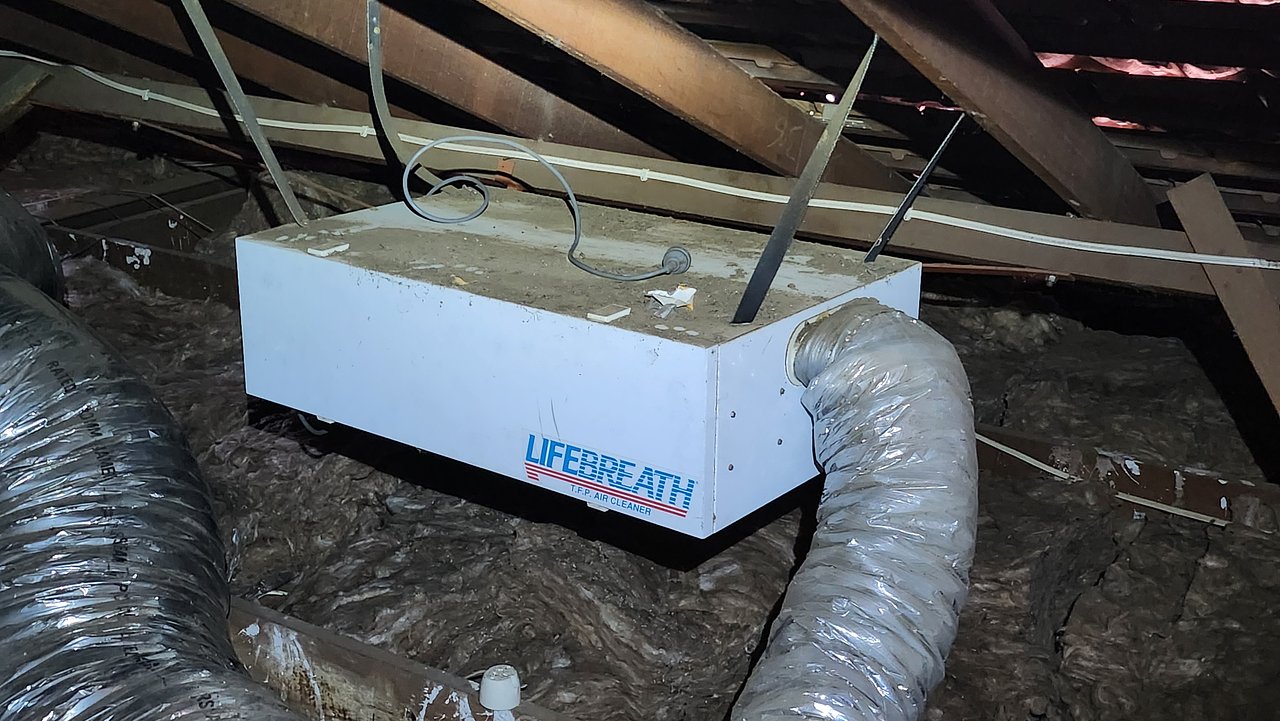
Sophie Murday Sun 5 May 2024 2:25AM
Thinking we could go for a big snail blower (like the lasers) or a beefy inline “turbine fan” (also often used for laser extraction), it gives us plenty of overhead which we can use for resin and solder extraction, and then we can add flow restrictors if we need to decrease the amount going to the printer bench and XL.

Penny Wood Sun 5 May 2024 2:52AM
Check this link: https://www.nationallaboratorysales.com/blog/what-is-the-importance-of-fume-hood-face-velocity The face velocity is the wind speed through the opening into the cabinet, and having the face velocity too high isn't desirable. 0.3-0.5m/s recommended in that link, and in a few other places I've checked.
If the wind speed is too high it results in drafts, messes with some filaments like ABS, and potentially moves light-weight objects like paper around. The ABS issue is less of an issue though because we'd probably be printing on the Bambu, so within an enclosure, but more is still not more. Also higher air speeds mean higher costs.
The laser cutters actively produce smoke, which has its own gas pressure and will actively displace air away, so it's a different kettle of fish really. A very rough calculation I just did shows it produces 15 L of CO2 after cutting 100mm in 10mm thick MDF. You need to displace the produced gas which requires a considerable wind speed. Soldering and printing is more fine particles and a bit of off-gassing. The amount of gas is way less.
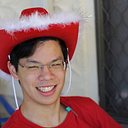
Lewis Yip Wed 8 May 2024 7:19PM
I'm not a mech eng or a HVAC person so take all below with a grain of salt.
I contribute that a typical exhaust blower for a laser cutter has specs below.
The nameplate figure for discharge (18m3/min) is at zero exhaust pressure.
The only datasheet (with pressure/airflow curve) I could find for a CZR80 was in Spanish, but the curve shows that airflow is essentially constant vs. pressure, which seems to be characteristic for centrifugal fans.
If you assume that the entire front of the 3D printer cabinet is open (0.66m * 2.4m) and that 0.5m/s² airflow is desired, you get a pretty ridiculous amount of CFM or m3/min required.
fume_hood_front_area = 0.66 m * 2.40 m
1.584 m^2 (area)
face_velocity = 0.5 metre/second
0.5 m s^-1 (velocity)
fume_hood_front_area * face_velocity
0.792 m^3 s^-1 (flow)
fume_hood_front_area * face_velocity -> cfm
1678.1529626051378087
fume_hood_front_area * face_velocity -> m^3 / min
47.52
fume_hood_front_area * face_velocity -> m^3 / hour
2851.2
If you reduce that to 1/4th the front of the 3D printer cabinet being open (i.e. because there are 4 sliding door panels, 1 of which is open) then you get 1/4th these numbers, which is something that 1x CZR80 fan could deal with.
If the enclosure has all doors closed, the centrifugal fan will try to increase pressure to maintain airflow and will probably pull a very high air speed through any small gaps.
Maybe an axial fan would be better, as airflow will drop rather than pressure increasing.
Again, not a mech eng!!

Penny Wood Thu 9 May 2024 1:10AM
@Lewis Yip because of having sliding doors, the most the cabinet can open will be 1/2 open at a time. Hmm.. looks like I did the calculations wrong above!

Ross Minney Wed 8 May 2024 6:16PM
Is the height of the roof going to play a factor into the equation of air speed and cfm? (Far from expert here)
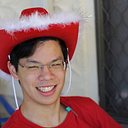
Lewis Yip Wed 8 May 2024 7:04PM
@Ross Minney I'm the wrong kind of engineer (mech eng needed) so take all following with a grain of salt.
With regards to height of the exhaust point, taking some very pessimistic assumptions (frictionless spherical cow in a vacuum), I get that about 120 W is needed to lift 1 m3/sec of air through 10 metres of height. That's not really that much power. Typical laser exhaust blowers are rated e.g. 550W. Again, I'm not a mech eng!
air = 1.225 kilogram / (metre^3)
1.225 m^-3 kg (mass_density)
height = 10 metre
10 m (length)
front_area = 2 metre^2
2 m^2 (area)
face_velocity = 0.5 metre/second
0.5 m s^-1 (velocity)
face_velocity * front_area
1.0 m^3 s^-1 (flow)
face_velocity front_area air height (9.81 metre / (second^2))
120.1725 m^2 s^-3 kg (power)
I recommend Frink for doing calculations like this (it tracks units, which makes it easy to explore calculations intuitively.)

Ross Minney Wed 8 May 2024 7:09PM
@Lewis Yip ew. Java. 😆
Penny Wood · Sun 5 May 2024 12:33AM
Am gonna go up into the roof now and have a look. Done enough procrastinating by typing this out to be ready to do it now! 😉